-
nanhai,foshan, CN 526200
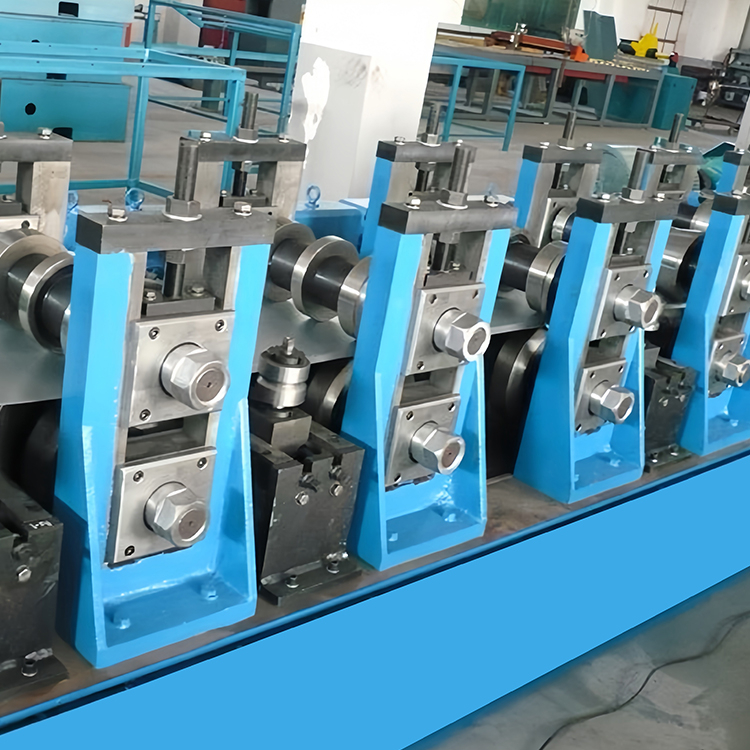
Understanding Roll Forming Machines
The Essential Tool for Metal Fabrication
In the world of metal fabrication, roll forming machines, such as roll formers, play a crucial role in shaping metal into various products. This article delves deep into the roll forming process, exploring its significance, applications, and benefits for manufacturers, especially those in the ventilation duct and door and gate industries. If you’re involved in these fields, understanding the capabilities of roll forming machines is vital. Read on to discover how these machines can enhance your production efficiency and product quality.
Table of Contents
What is Roll Forming?
Roll forming is a metal forming process that involves passing a strip of metal through consecutive pairs of rolls to create a desired cross-sectional profile. This continuous process allows for high precision and efficiency, making it ideal for producing long lengths of metal parts. For manufacturers like ventilation duct and door and gate producers, roll forming machines can significantly improve production rates while maintaining high-quality standards through effective machine maintenance.
The roll forming machine operates by deforming the metal strip incrementally at each pass, gradually shaping it into the final product. This method is not only suitable for thin sheets of metal but also for heavier gauge materials, showcasing its versatility across various applications.
How Does a Roll Forming Machine Work?
The operation of a roll forming machine involves several key steps. Initially, a coil of sheet metal is fed into the machine, where it is uncoiled and straightened. Following this, the metal strip enters a series of rollers designed to bend and shape it according to specific tooling.
Key Aspects of the Roll Forming Operation:
- Roll ToolingCustom-designed roll form tooling is essential to achieve specific profiles.
- Roll Stand Adjustment: Ensures proper alignment and spacing between rolls.
- Cutoff Mechanism: Allows for cutting the formed metal to the desired length.
Each component of the roll forming line plays a critical role in ensuring that the end product meets the necessary specifications and tolerances.
What Are the Benefits of Using Roll Forming Machines?
Investing in a roll forming machine offers numerous advantages for manufacturers:
- High Efficiency: Continuous production with minimal downtime.
- Versatility: Capable of forming various shapes from different types of metal.
- Precision: Achieves tight tolerances and consistent quality in the final product.
Using a roll forming machine can streamline your production processes, reduce material waste, and enhance overall product quality, making it an invaluable asset for any manufacturing plant.
What is the Roll Forming Process?
The roll forming process typically consists of several steps:
- Material PreparationThe metal coil is prepared for the roll forming process with attention to machine face alignment spacers.
- Feeding: The metal is fed into the machine and guided through the rollers.
- Forming: As the metal passes through the rollers, it is shaped into the desired profile.
- Cutting: The formed metal is cut to the required length.
Each stage is meticulously controlled to ensure that the final product adheres to the specifications, making it ideal for industries requiring high precision.
What Tolerances Can Be Achieved with Roll Forming?
One of the standout features of roll forming is its ability to maintain tight tolerances. Manufacturers can expect tolerances as fine as ±0.005 inches, depending on the material and design specifications. This accuracy is crucial for applications in ventilation duct systems and structural components, where even slight deviations can lead to performance issues.
Factors Affecting Tolerances:
- Material Thickness: Thicker materials may require more precise adjustments.
- Roll Tooling Design: Properly designed tooling ensures consistent results.
- Machine SetupAccurate setup and alignment, along with proper roll form tooling, are essential for achieving desired tolerances.
How to Choose the Right Roll Forming Machine?
Selecting the appropriate roll forming machine involves assessing several factors:
- Product SpecificationsUnderstand the profiles you need to produce using the roll former.
- Material Types: Ensure the machine can handle the specific materials you use.
- Production Volume: Choose a machine that meets your production capacity needs.
Consulting with an expert can help you navigate these choices, ensuring you find the right fit for your manufacturing operations.
What Are the Key Components of a Roll Forming Line?
A typical roll forming line consists of several essential components:
- Uncoiler: Holds and feeds the metal coil into the machine.
- Roll Forming Mill: The core of the operation, where shaping occurs.
- Cutoff System for roll form tooling.: Cuts the formed metal to length.
- Control System: Monitors and adjusts the operation for optimal performance.
Understanding these components can help you appreciate the complexity and precision involved in roll forming.
How to Maintain Your Roll Forming Machine?
Regular maintenance is critical to ensuring the longevity and efficiency of your roll forming machine. Here are some best practices:
- Routine Inspections: Check for wear and tear on rollers and tooling.
- Lubrication: Keep all moving parts well-lubricated to prevent excessive friction.
- Alignment Checks: Regularly verify the alignment of rollers to maintain product quality.
Investing in routine maintenance can prevent costly downtimes and ensure your roll forming operations run smoothly.
What Are Common Applications of Roll Forming?
Roll forming is widely used across various industries, including:
- Ventilation Duct Manufacturing: Creating ducts that fit perfectly in HVAC systems.
- Door and Gate Manufacturing: Producing frames and panels with high strength and durability.
- Automotive Components: Forming parts that require precise dimensions and structural integrity.
The versatility of roll forming machines makes them suitable for a wide range of applications, enhancing their appeal to manufacturers.
Why Should You Contact Us for Your Roll Forming Needs?
If you’re a ventilation duct manufacturer, door and gate manufacturer, or involved in related fields, our roll forming machines can elevate your production capabilities. We specialize in providing tailored solutions to meet your specific manufacturing requirements.
Our Commitment to You:
- Expert Guidance: Our team will help you find the right machine for your needs.
- Quality Assurance: We ensure that our machines meet the highest standards of quality.
- Customer Support: Our commitment to customer service means you’ll have support every step of the way.
Contact us today to learn how we can help optimize your roll forming operations!
Understanding Roll Forming Machines
What is the typical lead time for a custom roll forming machine?
Lead times can vary based on specifications, but typically range from 6 to 12 weeks.
Can roll forming machines handle different materials and maintain proper roll gap?
Yes, roll forming machines can work with various materials, including steel, aluminum, and other metals.
What is the average lifespan of a roll forming machine?
With proper maintenance, roll forming machines can last for decades, providing reliable service.
How does roll forming compare to other metal forming processes?
Roll forming is often more efficient for long runs and complex shapes compared to processes like stamping or bending.
What are the energy requirements for operating a roll forming machine?
Energy requirements can vary significantly depending on the machine size and production volume.
Summary of Key Points
- Roll forming is a highly efficient metal forming process ideal for various applications.
- Investing in a roll forming machine can enhance production efficiency and product quality.
- Regular maintenance is crucial for optimal machine performance.
- Our expert team is ready to assist you in selecting the right roll forming solution.
![Metal Siding Roll Forming Machine][]For more information on our offerings, explore these valuable resources:- Metal Siding Roll Forming Machine– Fully Automatic Box Beam Roll Forming Machine– Automatic C&U Channel Steel Stud And Track Keel Roll Forming Machine– Galvanized Punching Roll Forming Gate Door Machine– Windows Door Frame Gat Rolling Forming Machine By understanding the intricacies of roll forming, you can make informed decisions that enhance your manufacturing processes.